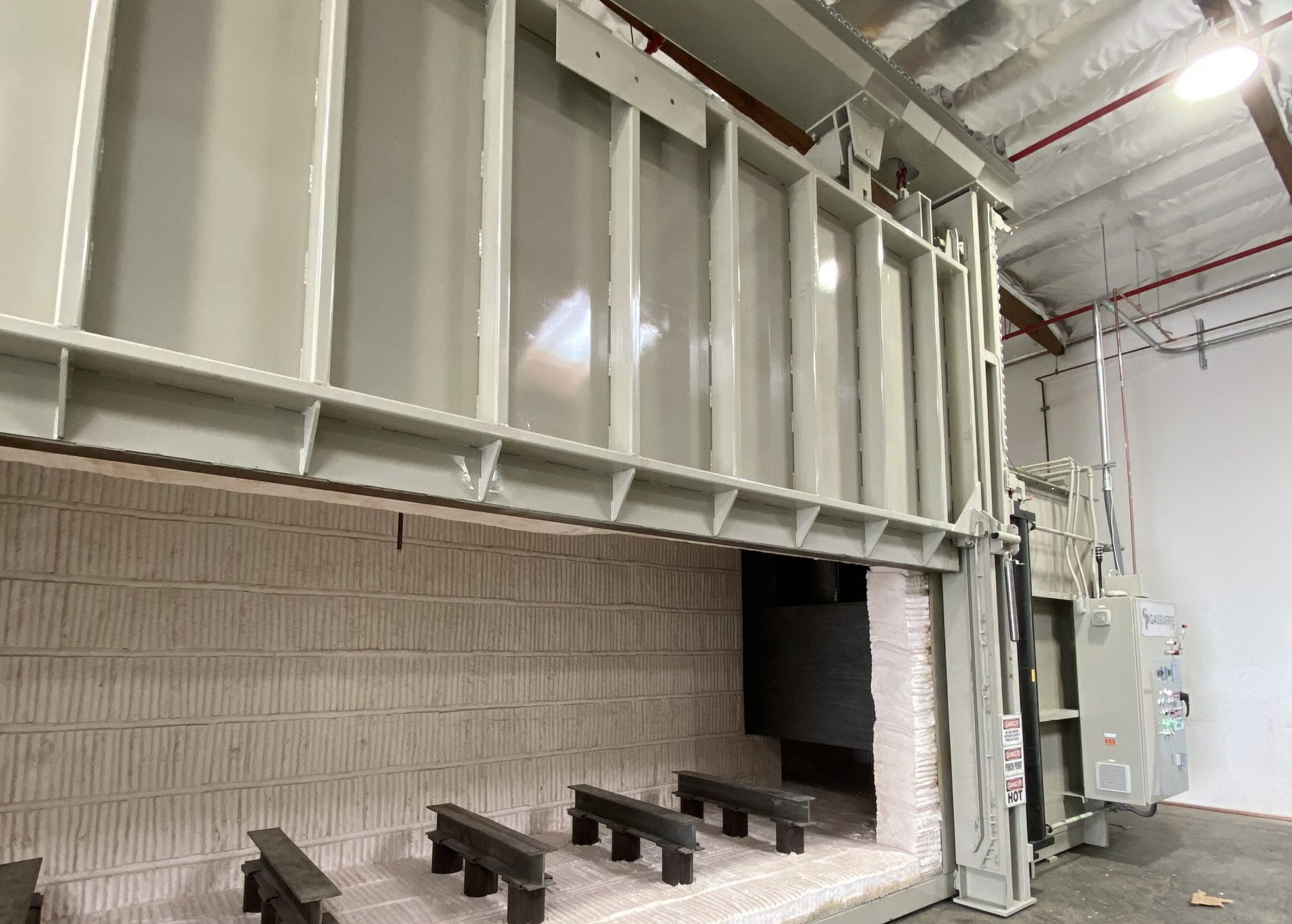
Precipitation hardening, also called age hardening is a heat treatment technique used to increase the yield strength of malleable materials, including most structural alloys of aluminium, magnesium, nickel, titanium, and some steels and stainless steels.
Unlike ordinary tempering, alloys must be kept at elevated temperature for hours to allow precipitation to take place. This time delay is called “aging”.
1. Solution annealing
The first step of precipitation hardening is called “solution annealing”. Its goal is to precipitate (or withdraw) metastable phases of alloys. In this process, inhomogeneities are transformed into homogeneities.
The metal is treated with a solution at high temperatures, slightly below the eutectic point of the material. Too low and the solution annealing is ineffective; too high and metals reach their melting point.
2. Quenching
Once the alloying materials are dissolved into the surface of the part, rapid cooling takes place until the solubility limit is exceeded. This prevents alloys from discharging. The solid solution after quenching is metastable, oversaturated and single-phased.
Typical quenching agents in precipitation hardening are water, oil and gas.
3. Aging
Aging is the last and most time consuming step of precipitation hardening. The solution is heated to an intermediate temperature. At temperatures between 150°C to 190°C (400°C- 500 °C for stainless steels), the part is held in a constant heat. The exact aging temperature depends on the composition of the material. The oversaturated solid solution transforms into two-phase alloys. The dominating phase is also known as matrix.