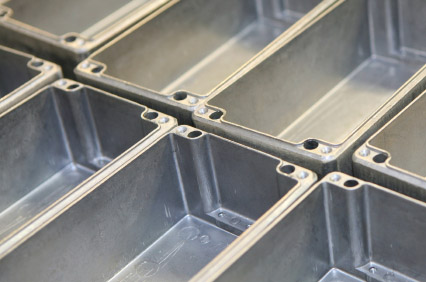
Aluminium is supplied in almost an infinite variety of shapes and sizes for use in industries as diverse as transportation (automobiles, aircraft, railcars), packaging (foils, food, beverage cans), building products (siding, structural) and sports equipment (bats) to name a few.
Aluminium has an excellent strength-to-weight ratio and is easily cast, fabricated, formed and machined.
The heat treatment utilizes alloying elements in the aluminum to further increase the strength and hardness for particular customer applications. A widely appreciated benefit of the hardening is the much improved machinability characteristics.
Step one
Called solution heat treatment, it is an elevated temperature process designed to place the soluble elements ‘in solution’. Rapid quenching, usually in water, follows this process. This temporarily ‘stabilizes’ the structure and for a short time renders the alloy very workable. It is at this stage that some fabricators retain this more workable structure by storing the alloys at sub-zero temperatures until they are ready to form them.
Step two
Called Artificial Ageing, this is done after quenching and the alloy is heated at an elevated temperature for a predetermined time. As a result of this, strengthening occurs and the properties are stabilized. This process is also called precipitation hardening, or artificial ageing.
By the total combination of, solution heat treatment, quenching, artificial ageing, and cold working, the highest strengths are obtained.
TO Temper – Annealed, recrystallised
T4 Temper – Solution heat treated, quenched, and naturally aged to a substantially stable condition. Mechanical properties and stability may change over a long period of time.
T5 Temper – Naturally cooled from the mould and then artificially aged to attain improved mechanical properties and dimensional stability
T6 Temper – Solution heat treated, quenched and artificially aged to attain optimum mechanical properties and generally good dimensional stability
Wrought Grades
Wrought aluminum alloys can be divided into two categories: non-heat treatable and heat treatable.
Non-heat-treatable alloys, which include the 1xxx, 3xxx, 4xxx and 5xxx series alloys.
Heat-treatable alloys include the 2xxx, 6xxx and 7xxx series alloys and are strengthened by solution heat treatment followed by precipitation hardening (aging).
Castings and Forgings
Cast aluminium alloys or Forgings are used in either as cast/ forged or heat treated conditions.
Forging Grades of aluminium are usually similar to grades supplied for heat treatment from wrought materials.
Castings grades vary from 3xxx to 6xxx and 7xxx series alloys. These grades can have additives to the virgin aluminium base to aid in grain refinement and adding further mechanical ability to the cast metal for suitable applications.
The size and shape of items that can be treated depends on the type of equipment operated by the heat treater. For large items, check the availability of suitably-sized facilities at an early stage
All of the following information should be included if possible. If uncertain, ask your heat treater before producing a specification:
- The process: TO, T4, T4X, T5, T6, T6X ect
- Material: type, grade, and the standard from which it is drawn, with drawing, composition and mill certificate where available.
- Any general standards applicable (national, international or company) that contain relevant details which must be adhered to.
- Existing condition; e.g. details of any prior heat treatment, such as hardening and tempering, solution treatment and ageing, intended to establish mechanical or other properties.
- The type(s) of testing required; e.g. hardness (Vickers, Brinell), tensile etc. and any special locations for testing or the removal of samples for test pieces.
- Requirements for any special certificates or data to be provided by your heat treater.
Guidance and information is always available from our experience heat treatment professionals.
Our procedures and work instructions are fully documented under our AS 9100 and ISO 9001 quality management systems.